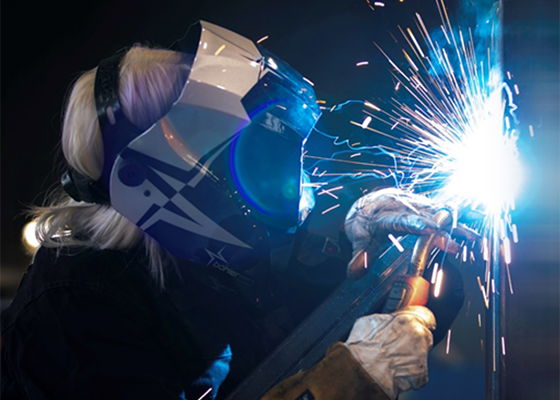
More than 100 different welding methods from MIG and MAG to laser
Welding as a joining method has been around for centuries, the use of industrial gases to optimise welding processes dates back to the 40s and 50s. Today, roughly 100 welding methods are used in different industry sectors. Since then the gas based welding processes have emerged to be the predominant group of welding methods. Important gas-shielded welding methods are MIG, MAG, TIG and plasma. Innovations boosted in the 80s and 90s with laser, tandem and laser-hybrid welding.
Welding as an essential process in many industries
Various techniques are used to melt and fuse metals, steels and alloys. Arc welding, as the most common fusion-based joining method, uses the heat generated by an electric arc struck between an electrode and a workpiece to melt and fuse metal in the joint area.
In all welding processes, the shielding and process gases, their exact compositions and their purity levels play a key role in influencing weld quality and productivity.
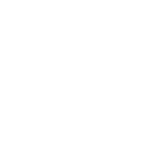
Oxygen, nitrogen, argon and carbon dioxide – the main welding gases
Oxygen, nitrogen, argon and carbon dioxide are standard or bulk gases that are used in process and manufacturing industry today. However, in many gas solutions or applications gas mixtures are commonly used. With premium gases like MISON® shielding gas you can increase the quality or your product, the productivity of your labour and the profitability of your business.
For any welding process, it is important to choose the right shielding gas. We provide an extensive shielding gas range to meet all requirements.
For gas welding, gas cutting, soldering and other fuel gas processes.
Buy here →
For TIG and plasma welding, and for root protection as well as for applications that require an inert
atmosphere.
Buy here →
For MAG welding (most suitable for so-called short-arc welding).
Buy here →
82% Ar + 18% CO2
- Shielding gas (short arc and spray arc) for MAG welding of unalloyed and low-alloyed steel
- Also suitable for cored wire electrodes.
Buy here →
92% Ar + 8% CO2
- Shielding gas for MAG welding of unalloyed and low-alloyed steel with spray arc.
Buy here →
75% Ar + 25% CO2
- For MAG welding of unalloyed and low-alloyed steel.
- Suitable for short arc MAG welding
Buy here →
90% Ar + 5% O2 + 5% CO2
- For MAG welding (spray arc) of unalloyed and low-alloyed steel.
Buy here →
69% Ar + 30% He + 2% O2
-For MAG welding of stainless steel.
Buy here →
98% Ar + 2% O2
- For MAG welding of stainless steel.
Buy here →
90% N2 + 10% H2
- Reducing root protection gas for TIG and MIG/MAG welding of e.g. stainless steel pipes.
Buy here →
82% Ar + 18% CO2 with 0.03% NO
- Working environment-friendly (ozone-reducing) shielding gas (spray arc) for MAG welding of unalloyed and
low-alloyed steel
- Also suitable for cored wire electrodes-
Buy here →
98% Ar + 2% CO2 with 0.03% NO
- Working environment-friendly (ozone-reducing) shielding gas for MAG welding of stainless steel.
Buy here →
75% Ar + 25% CO2 with 0.03% NO
- Working environment-friendly (ozone-reducing) shielding gas for MAG welding of unalloyed and low-alloyed
steel (suitable for so-called short arc welding).
Buy here →
92% Ar + 8% CO2 with 0.03% NO
- Working environment-friendly (ozone-reducing) shielding gas (spray arc) for MAG welding of unalloyed and
low-alloyed steel.
Buy here →
Argon with 0.03% NO
Working environment-friendly (ozone-reducing) shielding gas for TIG welding.
Buy here →
Argon with 0.03% NO
- Working environment-friendly (ozone-reducing) shielding gas for TIG welding.
- Cylinder with integral valve.
Buy here →
98% Ar + 2% H2 with 0.03% NO
- Working environment-friendly (ozone-reducing) shielding gas for TIG welding.
Buy here →
For plasma and laser cutting as well as root protection for TIG welding and applications that require a
reaction-inert (mainly inert) atmosphere.
Buy here →
Odorized oxygen for gas welding, gas cutting and soldering.
Buy here →
79% nitrogen + 21% oxygen. For applications that require clean and dry air.
Buy here →
65% Ar + 35% H2
- For plasma cutting of stainless steel.
Buy here →
95% Ar + 5% H2
- For TIG and plasma welding of austenitic stainless steel.
Buy here →
30% Ar + 70% He
- For TIG and MIG welding of certain stainless steel, aluminum and copper alloys in larger material
thicknesses as well as for plasma welding of aluminum and copper
Buy here →
Welding related areas
The big advantage of acetylene lies in the reducing effect of the welding flame, which is easy to adjust as well
as to control. Gas welding with acetylene is characterized by good gap-bridging capabilities. There is no, or very
little, joint preparation required. The problem-free application is particularly useful in out-of-position
welding.
In pipeline construction, for instance, where other welding methods are usually out of the question or not
economical, the oxy-acetylene flame is the welder’s reliable and true friend. Combustion of acetylene with oxygen
is characterized by a sharply defined flame cone.
We have developed a RAPID PROCESSING® concept for high productivity MAG welding, which creates better productivity as a consequence of higher welding speed and/or greater deposition rate. It also decreases less spatter and weld surface slag, better side penetration and smoother weld reinforcements. The technique is eminently suitable for welding non-alloy and low-alloy steels with thicknesses above 1 mm and can also be used on stainless steels. For the best results, unconventional welding parameter settings are used together with an argon-rich MISON® shielding gas, which provides greater productivity and a better working environment.
Plasma arc technique is reminiscent of TIG welding, where electric arc burns between a tungsten electrode and the
work piece. The most important difference is that the arc in plasma welding is forced through a restriction in the
form of a water-cooled nozzle.
The greatest advantage of plasma welding is visible on 2 to 8 mm plates with ‘key-hole’ technique, which involves
a powerful plasma arc melting a hole through the plate. When the burner is moved forward, material is also melted
in front of the hole. This material is forced towards the back of the hole by the arc pressure, where it moves
together due to surface tension and solidifies. A homogenous weld is created and complete full-penetration welding
is attained.
Depending on which gas is used, the shielding gas can have a clear effect on the arc energy. Normally, shielding
gas and plasma gas is the same. A root protection gas protects the molten weld pool and the area affected by the
heat on the root side of the weld.
TIG welding method is most often used for welding thin materials (~ 0,3–3 mm). The heat source is an electrical
arc that is generated between the work piece and the tungsten electrode. The pool and the electrode are protected
by a shielding gas which flows from a gas cup in which the electrode is centrally placed.
The shielding gas protects the electrode, the weld pool and the heated material against the damaging effects of
air and also affect the properties of the arc (e.g. the energy) and the appearance of the weld, as well as
productivity and working environment.
An inert gas such as argon, helium or a mixture of the two is most commonly used as shielding gas. Occasionally,
hydrogen and/or nitrogen are added in low concentrations. The welder must also be protected against toxic gases
and welding fume. MISON® shielding gases protect both the welder and the weld by reducing the emission of damaging
ozone
The method is very similar to MIG / MAG welding. The biggest difference is the addition material melting point,
since the base material does not melt at MIG brazing. Heat input in MIG brazing is considerably less than in MIG /
MAG welding, therefore is MIG brazing particularly suitable for welding of zinc coated sheets in such areas as the
automotive industry.
Argon is often used although small amounts of carbon dioxide and oxygen can be added to improve productivity and
properties.
In pipeline construction, for instance, where other welding methods are usually out of the question or not
economical, the oxy-acetylene flame is the welder’s reliable and true friend. Combustion of acetylene with oxygen
is characterized by a sharply defined flame cone.
MIG (metal inert gas) and MAG (metal active gas) welding methods are widely used in Western Europe, the United
States, and Japan due to their high productivity and ease of mechanization.
In MIG/MAG welding, filler metals in the form of solid wire or tubular-cored wire electrodes are melted off
continuously in an electric arc generated by a welding power source. The arc and molten weld pool are protected by
shielding gases, either inert (e.g., argon, helium) or active (e.g., argon/carbon dioxide, argon/oxygen), which
optimize the welding process and properties of the finished product. We offer MISON® shielding gases for optimal
welding applications and emphasizes safety measures for welders, including good ventilation and protection against
ozone emissions. Safety instructions for working with extreme heat and shielding gases are also provided.
In pipeline construction, for instance, where other welding methods are usually out of the question or not
economical, the oxy-acetylene flame is the welder’s reliable and true friend. Combustion of acetylene with oxygen
is characterized by a sharply defined flame cone.
Laser welding is gaining popularity in industrial applications. High productivity and quality are contributing factors to the increased use.
Examples of applications are welding of automotive components, transmission parts, heat exchangers and
tailored blanks. Lasers are also used for welding of medical equipment and lately, also battery components.
The CO2 lasers are now often replaced by multiple kilowatt fibre and diode lasers enabling the possibility to
guide the laser beam via optical fibres in combination with robots for 3D applications.
The laser beam is focused on the metal to be joined causing the material to melt and in some cases vaporize.
The welding process is performed as heat conductive or key-hole welding depending on the need for penetration and weld width.
Heat conductive welding can be utilized using CO2-, fibre and diode lasers. Deep penetration welding, also known as key-hole
welding often demands high laser power (multi kilowatt). Fibre and CO2 lasers are used for this application.
Welding gases protect the weld pool, optics, and control plasma formation. Some gas mixtures also interact
with the molten metal, improving productivity and weld quality. Our LASERLINE® gases offer optimal solutions for all processes.
- Gas welding
- Advanced welding processes
- Plasma welding
- TIG welding
- MIG brazing
- MIG-MAG welding
- Laser welding
Gas welding – one of the major processes in metal work
The big advantage of acetylene lies in the reducing effect of the welding flame, which is easy to adjust as well as to control. Gas welding with acetylene is characterized by good gap-bridging capabilities. There is no, or very little, joint preparation required. The problem-free application is particularly useful in out-of-position welding.
Shielding gas guide
choose the correct welding gas for your process
Do you know which shielding gases best match your welding methods and materials? Now you can find out easily and quickly. Our shielding gas guide helps you choose the right shielding gas for your welding process from MIG/MAG welding to TIG.
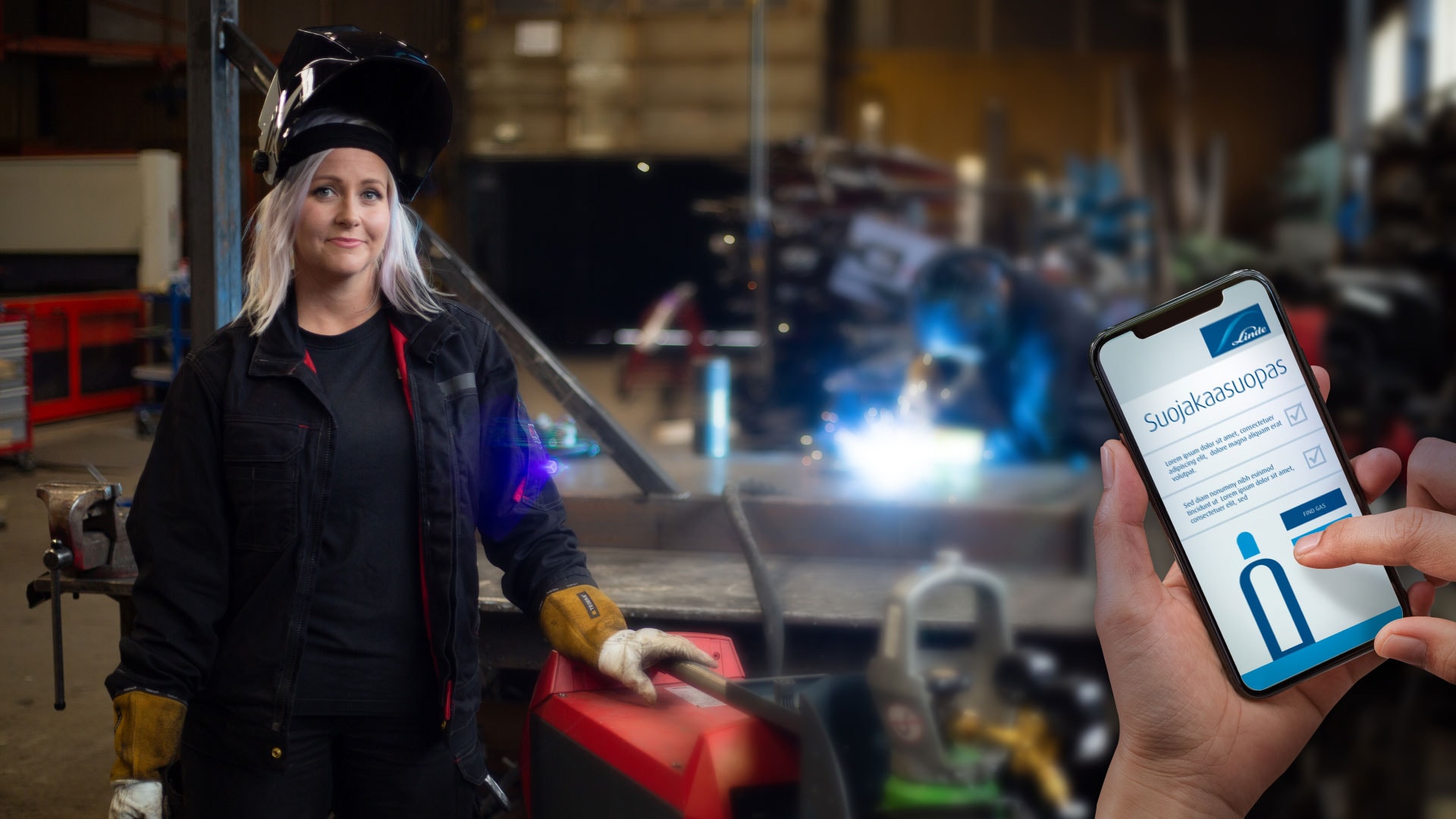
What do our customers say?
“Ozone is not good for the human organism, it’s bad for the respiratory system, it
damages you. There’s also a personal dilemma. When you get to know, them you don’t want the people you know to get
sick, because you care for them. It’s my friends and colleagues”
Abraham Bergman
Workshop Manager, SITAB